This combination of properties means that we have a ceramic that is appropriate for the toughest application conditions. Silicon nitride ceramics are therefore ideal for machine components with very high dynamic stresses and reliability requirements.
The manufacture of dense silicon nitride ceramic starts with sub-micron Si 3N 4 powder mixed with sintering additives (Al 2O 3, Y 2O 3, MgO etc.), and is sintered at temperatures between 1,750 and 1,950° C after moulding. Due to the decomposition of Si 3N 4 to Si and N 2 above approximately 1,700° C at atmospheric pressure, the N 2 pressure is increased during sintering in order to counteract this decomposition.
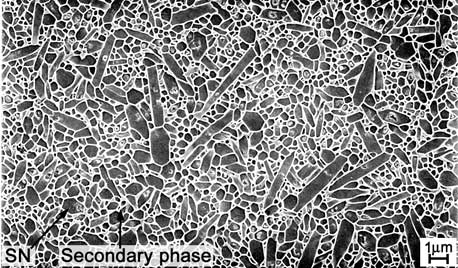
Figure 39: Microstructure of a gas-pressure sintered
silicon nitride
A relatively economical version is that of low-pressure sintered silicon nitride (SSN), which has medium bending strength, and from which high-volume components (e.g. for metallurgical purposes) can be manufactured.
Gas pressure sintered silicon nitride (GPSSN) is sintered in a gas pressure sintering furnace with an excess N 2 pressure of up to 100 bar. This creates a high performance material suitable for high mechanical stresses.
Hot pressed and hot isostatic pressed silicon nitride (HPSN and HIPSN) undergo even higher pressures of up to 2000 bar during the sintering process. HPSN and HIPSN are distinguished by even greater mechanical strength, compared to GPSSN, because the remaining porosity is almost completely eliminated by the high mechanical pressures involved in the manufacturing process. The limited geometries available with axially pressed HPSN (due to the use of a mechanical pressing punch) and the high manufacturing costs of HIPSN are disadvantages associated with this ceramic.
Important fields of application for components made from this dense silicon nitride material are metal processing with cutting tools (indexable cutting inserts), roller bearing technology using balls, rollers or rings, and machine construction involving highly stressed machine elements. The inclusion of such parts also in the field of metal forming illustrates the capacities of the material.
Reaction bonded silicon nitride (RBSN) is manufactured using a completely different approach. As an alternative to the high priced Si 3N 4 powder, the relatively economical Si powder is used here as a raw material. It is formed and nitrided in an N 2 atmosphere at temperatures of approximately 1,400° C to form Si 3N 4 - and there is no shrinkage! The resulting ceramic displays good mechanical properties, but is prone to oxidation at high temperatures due to its very fine open porosity.
Examples of the application of RBSN include kiln furniture, melting crucibles and ingot moulds as used, for instance, in the manufacture of silicon components for solar technology.
The addition of additives to the Si powder allows the nitrided Si 3N 4 to be densely sintered (sintered RBSN = SRBSN). Both versions of the material are, only suitable for materials with thicknesses of up to 20 mm, depending on the particular process, however.

Figure 40: Surface of a reaction bonded silicon nitride
The silicon aluminium oxynitrides (SIALON) are versions of silicon nitride ceramics. The raw material is blended from silicon nitride, enriched with materials including the metal oxide Al 2O 3, in order to synthesise specific mixed crystal forms that achieve properties similar to those of silicon nitride but at lower sintering temperatures. The mechanical properties can be adjusted over a wide range by modifying the type and quantity of the additives. The relatively high fracture toughness should be noted. SIALONs are therefore frequently used for cutting tools. Their low wetting by aluminium and other molten non-ferrous metals has made the SIALONs the de facto standard material for thermocouple protection tubes in the smelting industry.
Aluminium nitride (AlN) has a remarkably high thermal conductivity, with 180 Wm -1K -1 being standard, and > 220 Wm -1K -1 being achievable. Because this is combined with good electrical insulating properties, aluminium nitride is exceptionally suitable for applications in electrical engineering. In addition to this, aluminium nitride ceramics can be metallised by any of the usual processes, and thus can be prepared for brazing or soft soldering. Because the thermal expansion of aluminium nitride is similar to that of silicon, mechanical stresses created between these two materials under conditions of thermal stresses remain particularly small.
Because the material is suitable for further processing with both thick and thin film technology, and because it can be coated with copper through both the DCB (direct copper bonding) and the AMB (active metal brazing) processes for tracks greater than 1 mm in height, aluminium nitride is an ideal material for applications in telecommunications technology.
Aluminium nitride ceramic is therefore used as a substrate for semiconductors, as well as for high-power electronic parts, housings and heat sinks.
High resistance to gases such as are used in the preparation of silicon wafers means that aluminium nitride ceramics are also widely used in this sector.

Figure 41: Surface of an aluminium nitride
Aluminium nitride ceramics are particularly suitable when the application requires