7.1 The Design Sequence
The task of an engineer is the solution of
a technical problem. This solution must both fulfil the technical
specifications and must be economically feasible. It is absolutely
necessary that both these conditions are met. This means that
a compromise must be found between improved performance and
the required expense. Solutions that either do not guarantee
the technical function or that are too expensive are unsatisfactory.
In a good design that is appropriate for ceramics, the advantageous
properties of the ceramic materials are maximised and the
disadvantages (such as brittleness) are minimised or even
nullified through the use of good design principles (for example,
separation of functions, modular techniques, compressive loading,
etc.).
During the planning phase, information concerning the exact
function of the part to be designed and the properties of
the ceramic materials under consideration must first be obtained.
It is thus helpful if the design engineer and the manufacturer
work together at the earliest possible stage of the planning
phase, in order to decide on the fundamental feasibility of
the construction. Not only must the technical specifications
be taken into consideration, but also manufacturing costs,
including planning and development, so that the possibility
of wasted investment is detected as early as possible in the
design process. It is particularly advantageous when, on one
hand, the design engineer already possesses knowledge of designing
with ceramics, and on the other hand if the component maker
has an understanding of the sequence of the customer's operations.
A valuable prerequisite for reaching a decision regarding
the technical feasibility and for the purposes of cost calculations
is a complete and correct drawing. With reference to the first
design with which the design engineer approaches the ceramic
manufacturer, it is desirable for all the variable parameters
(shape, dimensions, tolerances, surface quality, etc.) be
clearly emphasised. The same is true for any dimensions whose
maintenance is crucial to the design.
The way in which the component will function, and the stresses
to which it will be subject, should be explained in the initial
discussions with the ceramic manufacturer, so that the optimum
ceramic material for the particular case can be chosen. As
a second step, the variable parameters mentioned above should
be discussed with reference to the ultimate function, so that
both sides become clearly aware of any difficulties that might
arise.
During the first meeting between the user and the component
manufacturer, figures concerning the expected lot sizes should
be available, since these are decisive for the choice of manufacturing
process to be used, and therefore for the expected manufacturing
costs. Small lot sizes, single parts and prototypes are often
machined from a preform, while the construction of expensive
tools, for example, for dry pressing, extrusion or injection
moulding, are only cost-effective with large batch sizes.
Parts manufactured using different processes do not necessarily
possess identical properties, a fact which must also be taken
into consideration when transferring experimental results
to ordinary manufacturing conditions (density gradients, tolerances,
wall thicknesses, taper, internal stress, taper etc. for example).
On the basis of the drawings with which he has been provided
and of discussions held with the user, the component manufacturer
is able to suggest changes that are necessary because of the
production technology. These changes frequently do not have
any effect at all on the function of the part, but are often
necessary to make it at all possible to manufacture the part,
or offer a reduction in costs without which economical manufacture
would not be possible.
As a rule, a few sample parts are manufactured and tested
after the modified design drawings have been discussed and
approved. On the basis of experience that can be obtained
from field tests using these parts a decision is reached as
to whether the production order can begin or whether the part
must be modified once again.
There can be differences between the properties of the prototype
and the Mass Prod.s part. Tests prior to final approval should
therefore use samples produced in a way similar to full production.
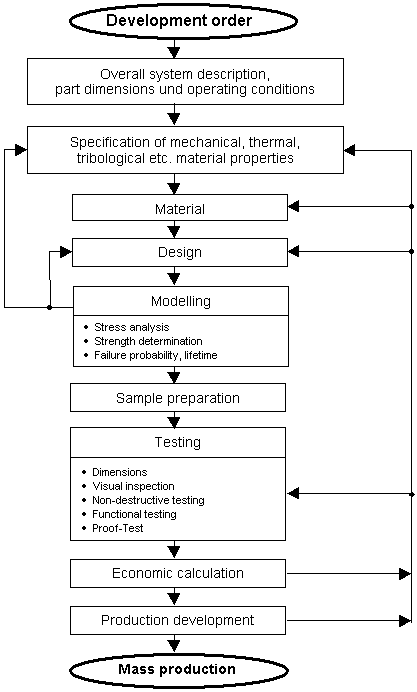
Figure 130: The development of ceramic components
|
|