|
|
|
|
7.6 Summary of Important Guiding
Principles
- Design with ceramic materials requires an approach fundamentally
different from design with metals. Different principles
of construction, calculation procedures and joining processes
must be applied.
- The integration of ceramic parts with a metallic system
results in different requirements from the ceramic part,
the assembly environment and the bond between the two. Compromises
are often necessary, and these may also lead to changes
in the metallic system.
- As a rule, copying a metal part or its exact conversion
to ceramic leads to failure.
- The advantages of using ceramic for the system should
be utilized as far as possible, while the weaknesses should
be avoided and unfavourable loading minimized.
- The properties resulting from the nature of the chemical
bonding in ceramics, which is the reason for their high
hardness, must be taken into account differently compared
with metals:
- brittleness,
- cracks and crack growth in the material,
- high scatter of strength data,
- low tensile strength,
- limited variety of forms and
- larger tolerances for non-machined parts.
- Finishing is typically time and cost intensive and should
thus be avoided, or at least reduced to a minimum.
- Very close cooperation with the ceramic manufacturer
is necessary, since the technical and economic implementation
using ceramics is even more demanding than with metals or
plastics.
An indicator for the cost of a part is the degree of difficulty
represented by the demands on a ceramic part. This can be
divided into five levels. A low level of difficulty should
therefore be aimed at if a cost-effective product is to be
obtained.
Degree
of difficulty |
Demands
on the
ceramic part
|
Design
is crucially influenced by |
1 |
- low mechanical stress
- application temperature
room temperature
|
forming process
(tooling costs, etc)
|
2 |
- as in 1 +
- specified dimensional and mould tolerances
|
forming process,
finishing (possibilities and costs) |
3 |
- as in 2 +
- specified surface quality
|
finishing
(possibilities and costs)
|
4 |
- greater mechanical stress
- and / or thermally
induced stress
|
stress distribution
in the part under load |
5 |
- as in 4 +
- Joining with other parts
|
forming and finishing
(dimensional and mould
tolerances, costs)
stress distribution in the composite under load
|
Table 24: Levels of difficulty
|
|
|
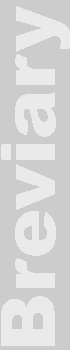 |