4.1.4 From
Forming to Firing
As a rule, green bodies made by a forming
process like casting, plastic forming and pressing, contain,
in addition to the ceramic powder mixture (including the permanent
additives), moisture and often organic deflocculants, plasticisers,
binders and other additives.
All components that are volatile at higher temperatures, i.e.
which vaporise or decompose, must be removed from the green
body with particular care before sintering in order to avoid
damage.
Depending on the powder, the shape of the part and its size,
and on the initial forming process, the green body incorporates
greater or lesser density gradients. After sintering it is
possible that these will make themselves noticeable in the
tolerances of the part.
Drying
All particles in a formed moist body are surrounded by a film
of water. The particles move closer together as the water
is removed and a volume reduction takes place; this is referred
to as drying shrinkage.
The drying shrinkage increases with increasing moisture content.
Shrinkage is also dependent on the grain size, the type of
raw materials and the forming process.
For example, the plate-like form of clay mineral particles
in extruded porcelain results in less shrinkage in the length
than in the cross-section. Such orientations, called textures,
must be taken into careful consideration when drying, according
to size and geometry of the ceramic product.
Different drying methods are applied depending on the particular
ceramic products.
Burning out
Green bodies formed from unfired material that is naturally
plastic are often sufficiently resistant to breakage in this
state. The resistance can, however, be improved with the aid
of organic additives. Such additives are, however, indispensable
when the unfired material is not plastic.
Burning out the remaining plasticisers and binders along with
other organic additives requires a carefully adapted temperature-pressure-atmosphere-time
profile in order to achieve a non-destructive and reproducible
removal of these additives from the finely porous green body.
One variation of burning-out is referred to as carbonising
or coking, for example with SiC. Here, organic components
are converted to carbon, which remains in the structure and
is converted, with the help of added reagents, to a ceramic
matrix during the sintering reaction.
After the drying and burning out (or carbonising/coking),
the structure of the green body (pressed powder with the shape
of component) is held together only by weak cohesive forces,
and requires particularly careful handling during the subsequent
process steps. For this reason, drying and burning out are
integrated with the sintering wherever possible.
Prefiring
In order to reduce the level of risk during handling, and
to allow the alternative white machining, the moulded green
body can be strengthened by firing with relatively low shrinkage
in preliminary firing. This requires strength and shrinkage
to be made reproducible through control of the process parameters.
Firing
The goal of ceramic technology is the manufacture of a mechanically
strong body able to withstand the widely differing requirements
and conditions of the application. There is only a small degree
of bonding between the particles of the green body. The ceramic
bonding, and the very high strength associated with it, is
obtained only by sintering at high temperatures. Firing allows
sintering (with or without a liquid phase) to take place,
and this is what actually creates the ceramic material.
The processes that occur during the sintering of the ceramic
body are very complex. The sintering rate is dependent on
purity, grain size, compaction and the sintering atmosphere.
Products made of oxide ceramics with very high purity sinter
via solid state reactions; they thus require much higher sintering
temperatures than bodies containing feldspar, such as porcelain,
that include a high proportion of glass phase material.
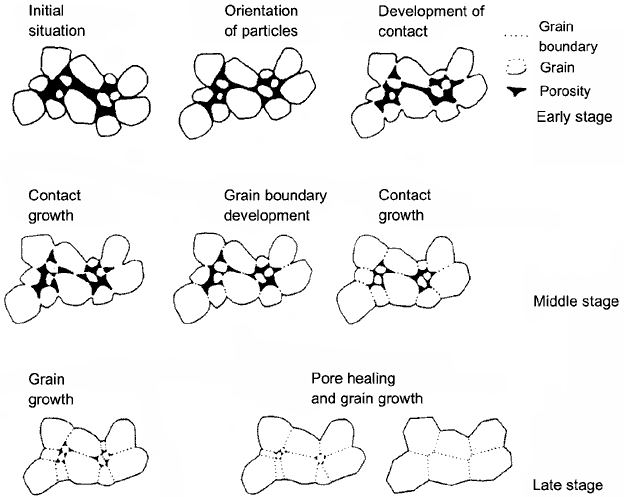
Figure 59: Grain growth during the sintering
process
Through reactions that occur during sintering,
a strengthening and densification of the ceramic takes place,
resulting in a reduction in porosity. This process results
in a volume reduction; this is called sintering shrinkage.
The amount of shrinkage for the various ceramic materials
is widely different.
Similar to drying, well-defined times and suitable atmospheres
are required when firing ceramic products. Disregarding these
can lead to increased internal stresses, to defects in the
part, and to unsatisfactory characteristics. Thinner shapes
and densely formed products behave better and can be sintered
faster than large ones with greater wall thickness.
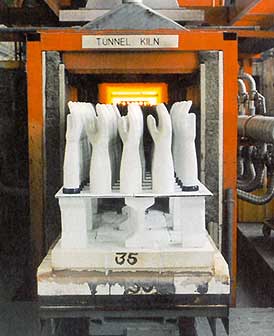
Figure 60: Tunnel kiln
Typical sintering temperatures:
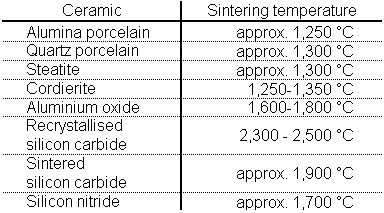
Table 5: Sintering temperatures of various
ceramic materials
The energy required for the sintering process increases disproportionately
as the firing temperature rises. In addition to the energy
input, the kiln furniture used to stack the green bodies in
the kiln is made of highly refractory material, and is a significant
cost factor.
Special varieties of material can be created
from some ceramic materials with the aid of particular types
of sintering process:
Hot pressing (HP)
is used to manufacture components with a density close to
the theoretical maximum. It is a sintering process supported
by uniaxial pressing.
Hot isostatic pressing (HIP)
allows small parts particular to achieve the maximum density
through the application of isostatic gas pressure of up to
3,000 bar at temperatures up to approximately 2,000°C
(usually within a collapsible silicate glass envelope).
|
|